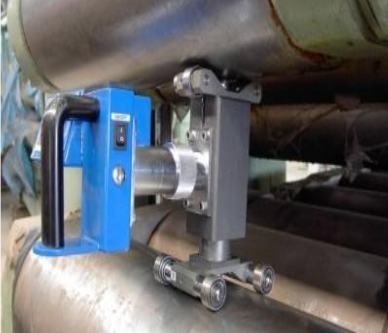
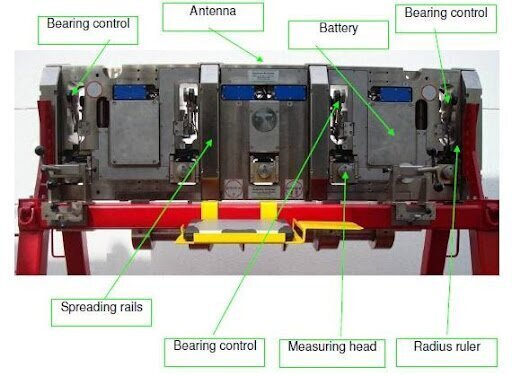
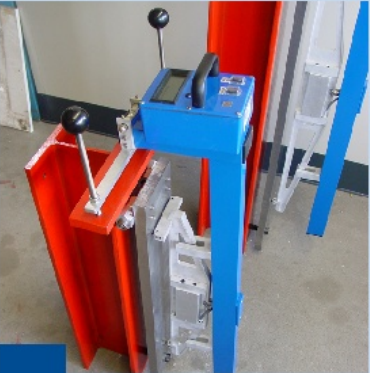
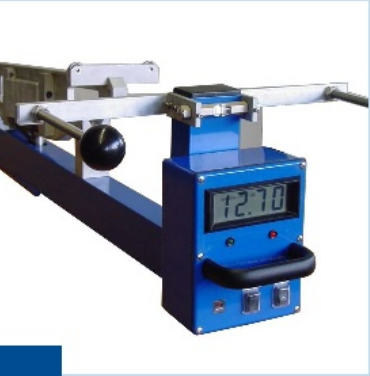
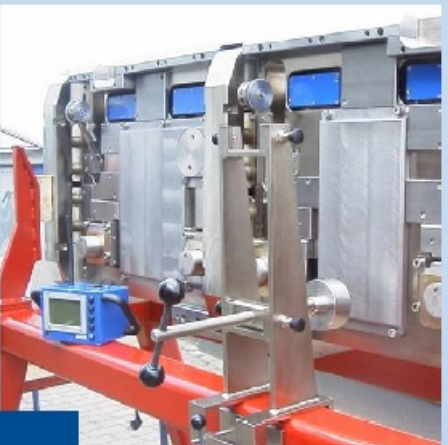
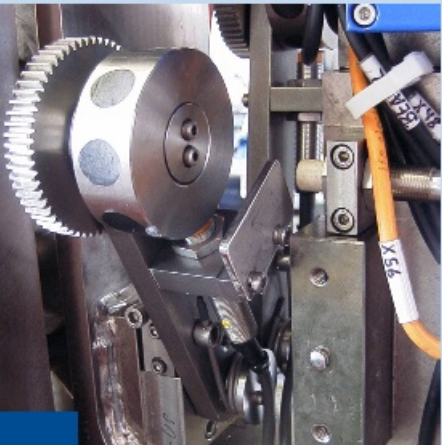
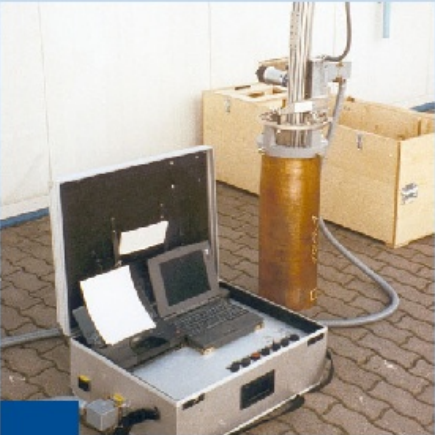
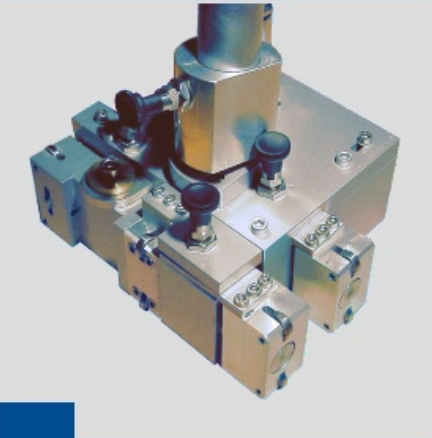
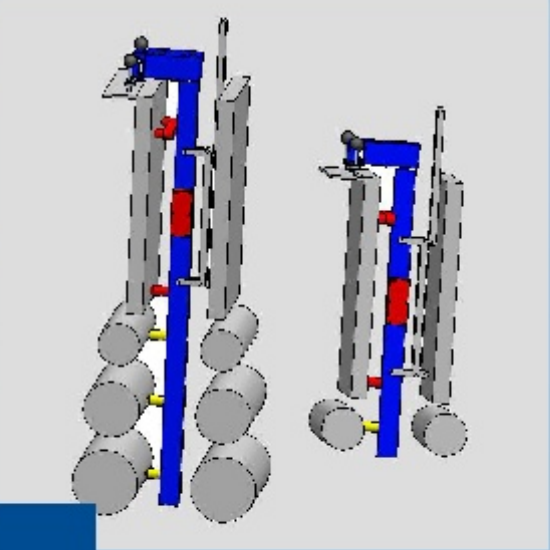

Roll Gap Checker
Roll Gap Checker the innovative strand condition roll checker has become an integrative element of quality control in modern continuous caster technology. Gaptor enables the control of all potential error sources and provides detailed information about the condition of the strand guidance. The survey of all quality relevant parameters like roll gap, roll rotation, roll bend and water spray allows for preventive maintenance actions which account for cost reductions.
Mould Tapper Guage
The taper measurement device MiniTap uses a high precision electronic together with an inclinometer connected to a self-centring mechanic. MiniTap allows an easy and precise determination of the taper of the narrow sides of the mould. The self centring mechanic ensures that the spacer is nestled up properly against the narrow side of the mould. By means of the bubble level and the adjustment screw, the device is positioned horizontally. MiniTap comes with a calibration device for periodical calibrations to allow reproducible results on a long term.
Other Customise Measuring Instruments
1.Strand Condition Monitoring Device
The innovative strand condition roll checker has become an integrative element of quality control in modern continuous caster technology. Gaptor® enables the control of all potential error sources and provides detailed information about the condition of the strand guidance. The survey of all quality relevant parameters like roll gap, roll rotation, roll bend and water spray allows for preventive maintenance actions which account for cost reductions. Gaptor® collects all necessary data within one measurement cycle. This avoids loss of time and difficult steric configurations as in manual measurements. The results of the periodic measurement runs can be compared. The factory operator is consequently in the position to plan for maintenance actions and replacement of a section of the caster machine
2.Mould Tubes:
MiniMould is designed to determine the inner dimensions of rectangular, square and round billet and bloom moulds. The periodical inspection of the mould dimensions is a fundamental element of quality control activities in the steel production. Wear and deformation can be monitored very early. Thereby preventive maintenance actions can be taken in an early phase to ensure cost savings. The measuring range starts from 120 mm up to over 800 mm with an accuracy of +/- 0.05 mm. Measurements can be taken at four lines at the same time. The results are displayed in a spreadsheet and a graphic sheet.
3.Foot Roller Alignment Checking Device:
The quality and safety of a continuous caster machine is highly affected by the correct vertical adjustment of the mould as well as by the relative alignment of the foot rollers. Therefore a measurement system has been developed which is capable of fulfilling both functions. Minifoot is a measurement system which enables the caster operator to check these parameters in an easy and fast way. Inserted into the mould displays the actual values of the vertical mould position and the foot roll alignment relative to the mould surface. Minifoot is available for curved moulds as well.